The customer
The customer is one of the world's largest producers and exporters of agricultural fertilizers. The company was building a 10 km conveyor transport system to deliver minerals from the extraction site to a processing plant. The customer needed to implement a distributed control system (DCS) as a part of the conveyor's automation system.
The customer put out to tender a DCS that would maintain the company’s standards for security and resilience and ultimately decided to go with Brimit’s solution.
Automating conveyor operations
- Monitoring conveyor sensors
- Controlling start and stop procedures
- Monitoring conveyor operation parameters
- Managing acoustic alarms and warning lights
Brimit’s system was integrated into the customer’s existing SCADA system using the Modbus RTU industrial protocol. The DCS carries out the tasks of remote control, comprehensive monitoring, and accident prevention on the conveyor. In an emergency, the system immediately halts operations at the necessary point along the length of the conveyor.
Brimit’s DCS keeps the conveyor running smoothly, minimizes the number of emergencies on the line, and reduces material and financial losses caused by accidents and downtime.
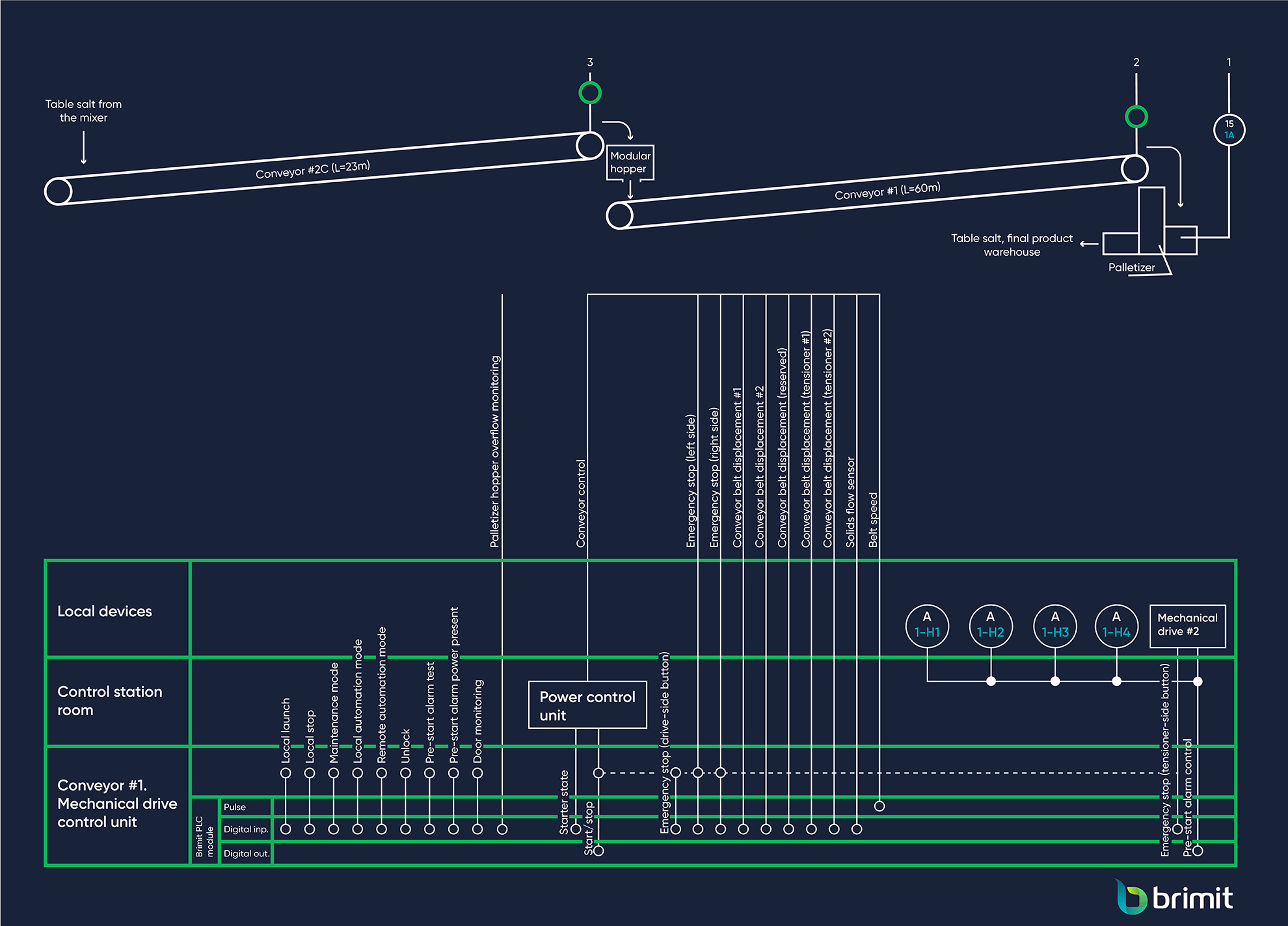
More about Brimit’s DCS
Brimit offers over 10 types of PLC and input/output modules. When used in combination, they make it possible to gather data from automation objects. With so many diverse configurations possible, the solution can be used in a wide range of different fields, including mining, fertilizer production, wood processing, engineering, and food production.
Brimit’s DCS supports multiple industrial and IoT communication protocols, including Modbus, OPC UA, and MQTT. Since we use standardized APIs, we don’t limit customers to a certain vendor's products.
The benefits of Brimit’s solution:
- Cost-effectiveness and repairability—Installing and replacing our devices won’t break the bank.
- Reliability—Our devices are designed to withstand harsh industrial operating conditions—for example, electromagnetic disturbances.
- High system capacity and scalability — Our DCS is highly flexible and can cover any industrial facility with sensors for setting up an automation system.
- No vendor lock-in—Our devices work with other vendors’ software and hardware according to industry-standard protocols.
- High-speed performance—Brimit’s controllers are guaranteed to respond to actions within the specified time frame, regardless of the number of modules on the automation object.